Working in Welding: The Ultimate Welding Terms Glossary
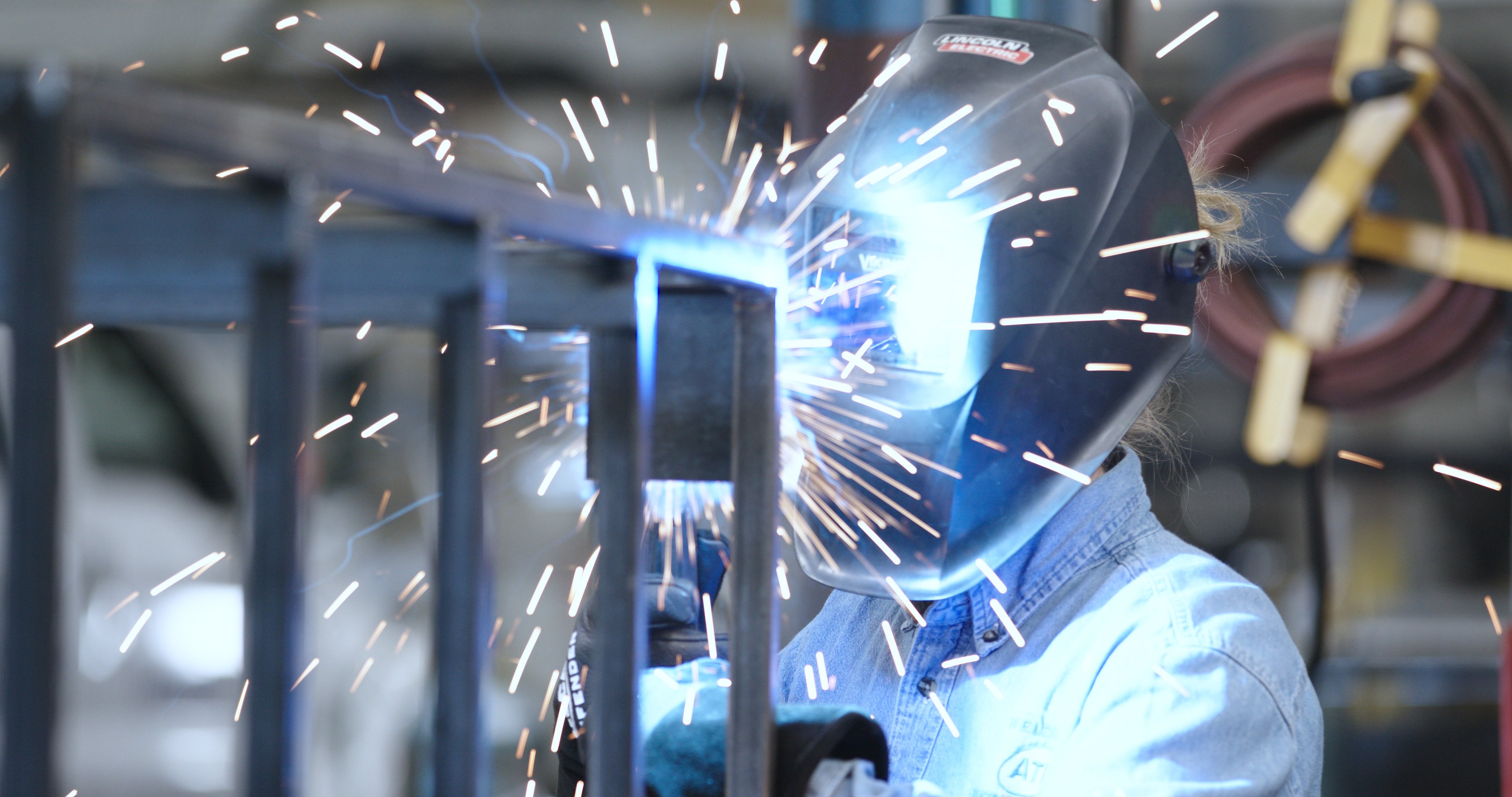
Working in Welding: The Ultimate Welding Terms Glossary
Welding is both a science and an art, requiring a blend of technical knowledge and practical skills. For newcomers, the array of jargon can be intimidating. However, understanding these terms is essential, whether you're embarking on a career in welding, managing welding projects, or diving into it as a hobby. This guide aims to help you grasp the foundational language of welding, providing insights to support your learning journey.
Disclaimer: This guide is informational and not a substitute for formal training or certification. Please consult accredited training programs for professional guidance.
-
Basic Welding Terms
-
Joints and Positions
-
Welding Processes
-
Defects and Testing
-
Tools of the Trade
-
Safety First
-
Why Understanding Welding Terms Matters
-
Conclusion
Basic Welding Terms
Arc:
The electric current that generates intense heat to melt the metal, forming the weld. The arc is the heart of many welding processes.
Example: In stick welding, the arc is created between the electrode and the base metal, producing enough heat to join them.
Base Metal:
The primary material being welded, which forms the foundation of the weld joint.
Example: Steel plates in construction projects are common base metals.
Electrode:
The component that conducts the current to the workpiece. It can be consumable (melts to fill the joint) or non-consumable (does not melt, as in TIG welding).
Example: A flux-coated stick electrode is used in shielded metal arc welding (SMAW).
Filler Material:
A material added during the welding process to fill gaps and create a strong joint.
Example: In MIG welding, a wire electrode doubles as filler material.
Fusion:
The process where heat melts the edges of materials so they can merge into a single, unified structure.
Importance: Proper fusion ensures the strength and durability of the weld.
Shielding Gas:
A protective gas (like argon or carbon dioxide) that surrounds the weld area to prevent atmospheric contamination.
Example: In TIG welding, argon is a popular choice due to its inert properties.
Joints and Positions
The configuration of materials and their positions significantly influence the welding process. Below are key concepts:
Types of Weld Joints
- Butt Joint: Two pieces of metal are joined end-to-end in the same plane.
- Lap Joint: Overlaps two pieces of metal, welding along their edges.
- T-Joint: Creates a “T” shape by welding one piece perpendicular to another.
- Corner Joint: Joins two metal pieces at right angles to form a corner.
- Edge Joint: Welds the edges of two pieces that are placed parallel.
.jpg?width=4096&height=2160&name=ATI-Welding-022720-%20(1).jpg)
Welding Processes
Welding offers numerous techniques tailored to specific applications. Here are the most common methods:
- MIG Welding (Metal Inert Gas): Also known as Gas Metal Arc Welding (GMAW), this method uses a wire electrode and shielding gas. It’s popular for its ease of use and speed.
- Applications: Automotive repairs, manufacturing, and construction.
- Benefits: Easy to learn and efficient for large projects.
- TIG Welding (Tungsten Inert Gas): Known for its precision, TIG welding uses a non-consumable tungsten electrode. It’s ideal for thin materials and detailed work.
- Applications: Aerospace, automotive, and artistic projects.
- Benefits: Produces clean and high-quality welds but requires skill.
- Stick Welding (SMAW): A traditional and versatile method using a consumable electrode coated in flux. It doesn’t require external shielding gas.
- Applications: Outdoor and industrial projects, particularly for heavy materials.
- Benefits: Works well in windy or outdoor environments.
- Flux-Cored Arc Welding (FCAW): Similar to MIG welding but uses a flux-filled electrode, which creates a shielding gas when melted.
- Applications: Heavy equipment repair and shipbuilding.
- Benefits: Effective on thicker materials and in outdoor conditions.
Defects and Testing
Common Defects
- Porosity: Caused by trapped gas during solidification, resulting in small holes within the weld.
- Cracks: Often occur due to stress or improper cooling.
- Undercut: A groove melted into the base metal beside the weld.
Prevention Techniques: Proper cleaning, adjusting welding speed and angle, and ensuring gradual cooling.
Testing Methods
- Non-Destructive Testing (NDT): Techniques like X-rays or ultrasonic testing allow inspection without damaging the weld.
- Destructive Testing: Cutting and examining weld sections to evaluate internal quality.
Tools of the Trade
Equip yourself with the right tools to enhance efficiency and safety:
- Welding Helmet: Protects against UV rays, sparks, and spatter.
- Welding Clamps: Secure workpieces in place.
- Chipping Hammer: Removes slag, a byproduct of some welding processes.
Safety First
Welding is inherently risky. Prioritize safety with these guidelines:
- Personal Protective Equipment (PPE): Fire-resistant clothing, gloves, steel-toed boots, goggles, and helmets.
- Ventilation: Ensure proper airflow to avoid inhaling harmful fumes.
- Fire Safety: Keep a fire extinguisher nearby.
Why Understanding Welding Terms Matters
Whether you're an aspiring welder, a project manager, or an enthusiast:
- Enhanced Communication: Speak confidently with colleagues and clients.
- Improved Efficiency: Choose the right methods and tools for each job.
- Better Safety: Recognize hazards and take proactive measures.
Conclusion
Mastering welding terminology is an important step in building foundational knowledge. Whether you're pursuing welding as a career or hobby, the right information can empower you to achieve success. Remember to prioritize safety, embrace learning opportunities, and consider formal training for further skill development.
Is a former student I enjoyed my time at ATI with my education I landed a job at Toyota
Posted by Jordan Harris on Friday, August 14, 2015
DISCLAIMER – Advanced Technology Institute (ATI) makes no claim, warranty or guarantee as to actual employability or earning potential to current, past or future students or graduates of any educational program offered. The Advanced Technology Institute website is published for informational purposes only. Every effort is made to ensure the accuracy of information contained on the AUTO.edu domain; however, no warranty of accuracy is made. No contractual rights, either expressed or implied, are created by its content.
Gainful Employment Information – Maritime Welding AOS Degree
Gainful Employment Information – Maritime Welding (Diploma)
For more information about Advanced Technology Institute or any of our programs click here: http://www.auto.edu/ or http://ow.ly/VoydP.
Industry Knowledge
Welcome to the Advanced Technology Institute's Blog, your resource for industry insights and discussions on technologies shaping the future of automotive, heavy vehicle, hvac, welding, and other related career paths.
Explore how ATI's curriculum and hands-on learning opportunities can propel your career in the tech-driven world.