Guide to TIG Welding
TIG welding, also known as Gas Tungsten Arc Welding (GTAW), is a precise welding method known for its ability to produce high-quality welds. It is widely used in industries requiring fine, clean welds such as aerospace, automotive, and art. This guide will cover the basics, techniques, uses, pros, and some challenges of TIG welding.
-
What is TIG Welding?
-
Equipment and Setup.
-
Welding Technique.
-
Applications for TIG Welding.
-
Materials Used in TIG Welding.
-
Advantages of TIG Welding.
-
Challenges and Solutions.
-
Tips for Successful TIG Welding.
-
Conclusion.
What is TIG Welding?
TIG welding uses a non-consumable tungsten electrode to produce the weld. The weld area is protected from atmospheric contamination by an inert gas, usually argon.
In TIG welding, an electric arc is formed between the tungsten electrode and the workpiece. The tungsten electrode, which has a very high melting point, does not melt during the process. Instead, the heat from the arc melts the base material and any filler metal used, creating a weld pool. The inert gas shield prevents oxidation and contamination.
Equipment and Setup
- TIG welder
- Tungsten electrodes
- Filler rods (if required)
- Shielding gas (argon or argon-helium mix)
- Welding torch
- Foot pedal or hand control for current adjustment
- Protective gear (helmet, gloves, jacket)
Setup Steps:
- Choose the Right Tungsten Electrode: Select the correct tungsten electrode for your material and current type. Thoriated tungsten is common for DC welding, while seriated or lanthanotid tungsten is used for AC welding.
- Prepare the Electrode: Sharpen the tungsten electrode to a point for DC welding, or leave it slightly rounded for AC welding.
- Set Up the Shielding Gas: Connect the gas cylinder to the welder and set the flow rate to around 15-20 cubic feet per hour (CFH).
- Adjust the Welder Settings: Set the machine to AC for aluminum and magnesium, or DC for steel, stainless steel, and other metals. Adjust the amperage based on the material thickness.
- Assemble the Torch: Insert the tungsten electrode into the collet and tighten. Attach the torch to the gas hose and power source.
Welding Technique
Steps to Perform TIG Welding:
- Clean the Workpiece: Thoroughly clean the workpiece to remove any oxides, grease, or contaminants. Use a dedicated stainless steel brush or chemical cleaners for aluminum.
- Strike the Arc: Use the foot pedal or hand control to start the arc. Hold the torch at a 10-15 degree angle to the workpiece.
- Create the Weld Pool: Move the torch in a small circle or back-and-forth motion to create a weld pool. For thin materials, a steady hand is crucial to avoid burn-throughs.
- Add Filler Metal: If using filler metal, dip the filler rod into the leading edge of the weld pool while maintaining a consistent arc length. Do not let the filler rod touch the tungsten electrode.
- Control Heat Input: Adjust the current using the foot pedal or hand control to maintain a stable weld pool. Too much heat can cause warping, while too little can result in poor penetration.
- Finish the Weld: Gradually reduce the current at the end of the weld to avoid crater formation. Release the foot pedal slowly to taper off the arc.
Applications of TIG Welding
Many industries use TIG welding. Some examples include the use in the aerospace industry where it is used for welding thin materials and critical components that require high precision and the automotive industry where it is ideal for welding exhaust systems, fuel tanks, and custom parts. Also, since it is aesthetically pleasing and has a clean appearance, TIG welding is used in art and sculptures. Lastly, it is used in medical devices because of its ability to ensure high purity and strength in stainless steel and titanium components.
Materials Used in TIG Welding
- Aluminum: TIG welding is commonly used for welding aluminum due to its ability to handle the material’s oxide layer and thermal conductivity.
- Stainless Steel: Produces strong, corrosion-resistant welds without compromising the material’s properties.
- Magnesium: Suitable for applications requiring lightweight and strong joints.
- Copper: Used in electrical applications due to its conductivity and high-quality welds.
Advantages of TIG Welding
There are many advantages of using TIG welding. Precision and control are two of the main selling points. TIG offers excellent control over the heat input and weld pool, allowing for precise, high-quality welds. In TIG welding, you can use a wide range of metals and thicknesses, making it suitable for various applications. It produces welds with minimal spatter and contamination, reducing the need for post-weld cleaning. Another advantage of TIG welding it that is has high-quality joints. It ensures strong, aesthetically pleasing welds that are critical for applications requiring high structural integrity. Also, in some cases, TIG welding can be performed autogenously (without filler metal), further reducing potential contamination.
Challenges and Solutions
Challenges:
- High Skill Requirement: TIG welding requires significant practice and skill to master due to the precision involved.
- Slower Process: Compared to other welding methods, TIG welding can be slower, making it less suitable for high-production environments.
- Sensitive to Contamination: The weld area must be meticulously cleaned to prevent defects.
Solutions:
- Training: Invest time in training and practice to develop the necessary skills.
- Proper Preparation: Ensure thorough cleaning and preparation of the workpiece to minimize contamination risks.
- Controlled Environment: Perform TIG welding in a controlled environment to maintain consistent conditions and reduce contamination.
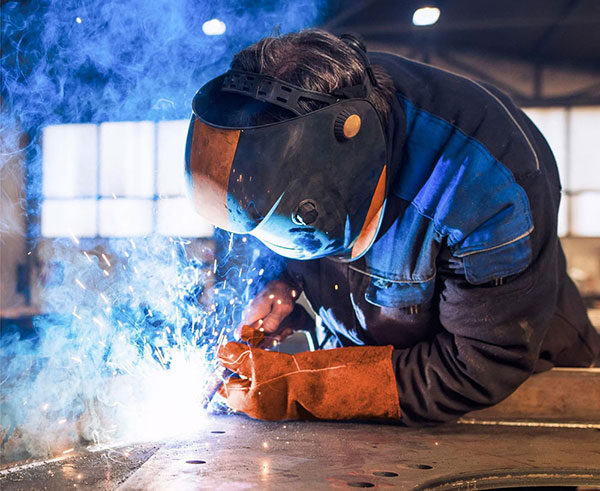
Tips for Successful TIG Welding
- Electrode Preparation: Properly prepare and maintain the tungsten electrode to ensure a stable arc. Use a dedicated grinding wheel to avoid contamination.
- Shielding Gas Management: Use the appropriate shielding gas flow rate to protect the weld pool from contamination. For aluminum, an argon-helium mix can improve heat transfer.
- Heat Control: Use the foot pedal or hand control to precisely adjust the heat input during welding, especially for thin materials.
- Joint Preparation: Ensure proper fit-up and alignment of the workpieces to achieve consistent weld quality.
- Practice: Consistent practice is essential to develop the muscle memory and hand-eye coordination required for TIG welding.
Conclusion
TIG welding is a highly versatile and precise welding method that excels in producing high quality and aesthetically pleasing welds. Its ability to weld a wide range of materials makes it invaluable in industries where precision and strength are paramount. Even though it requires a higher skill level and much preparation, the benefits of TIG welding make it a preferred choice for many critical welding applications.
If you are interested in learning more about ATI’s Welding program, click here.
Industry Knowledge
Welcome to the Advanced Technology Institute's Blog, your resource for industry insights and discussions on technologies shaping the future of automotive, heavy vehicle, hvac, welding, and other related career paths.
Explore how ATI's curriculum and hands-on learning opportunities can propel your career in the tech-driven world.